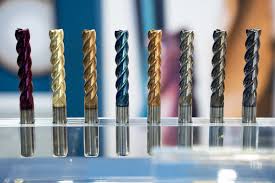
Tooling is at the heart of every machining operation. The right techniques can dramatically improve efficiency, reduce costs, and ensure high-quality output. Whether you’re a seasoned machinist or new to the field, understanding and applying the best tooling practices is crucial. In this guide, we’ll explore key techniques and tips to help you get the most out of your tools.
1. Selecting the Right Tool for the Job
Choosing the appropriate tool for each machining task is the foundation of efficient and precise operations. Factors like material hardness, type of cut (milling, drilling, turning), and the desired finish play critical roles in tool selection.- Material Compatibility: Ensure your tool material (e.g., carbide, high-speed steel) matches the workpiece material to avoid wear and tear.
- Tool Geometry: Consider the tool’s shape, angle, and size for the specific operation.
- Coatings: Utilize coated tools (e.g., TiN, TiCN, AlTiN) for enhanced performance, especially in high-speed or hard material applications.
2. Proper Tool Setup and Alignment
Correct tool setup and alignment are vital to prevent inaccuracies and tool breakage. Here are some best practices:- Secure Clamping: Always ensure that tools and workpieces are firmly clamped to prevent movement during machining.
- Alignment Checks: Use dial indicators or laser alignment tools to check tool positioning.
- Runout Minimization: Regularly inspect and adjust for runout to maintain concentricity, especially in high-precision tasks.
3. Optimal Cutting Speeds and Feeds
Speed and feed rates are critical to achieving the desired finish and tool life. Here’s how to get it right:- Calculate Correctly: Use speed and feed calculators tailored to your specific tool and material combination.
- Monitor Performance: Adjust speeds and feeds based on real-time monitoring of tool performance and workpiece conditions.
- Chip Load Management: Maintain appropriate chip load per tooth for milling operations to ensure efficient material removal without tool overload.
4. Tool Maintenance and Wear Monitoring
Regular maintenance extends tool life and ensures consistent performance.- Inspection Routines: Conduct frequent checks for wear patterns, chipping, or dull edges. Replace or regrind tools as needed.
- Coolant Use: Employ coolants effectively to reduce heat buildup and wear. Make sure coolant nozzles are properly positioned.
- Tool Storage: Store tools in a clean, dry environment, preferably in designated racks or containers to avoid damage.